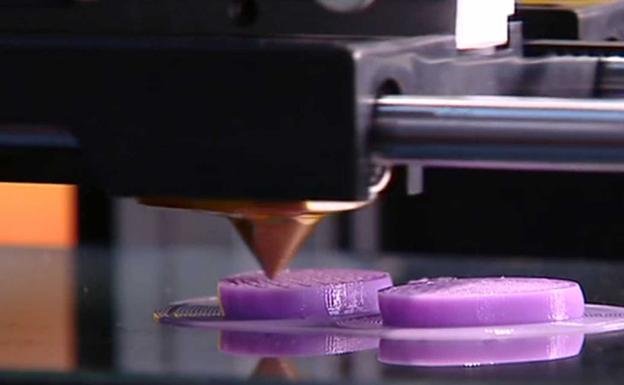
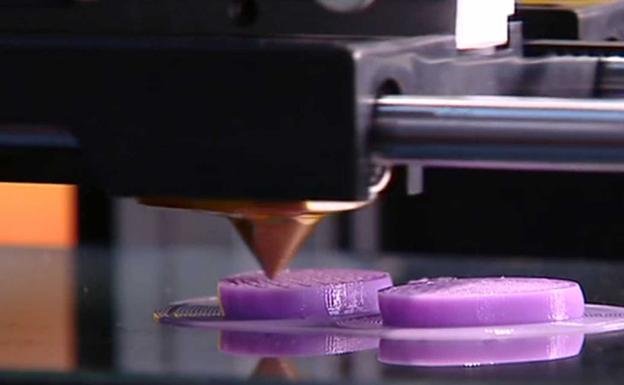
Secciones
Servicios
Destacamos
Edición
sara borondo
Lunes, 4 de marzo 2019, 01:31
Una de las tecnologías que más ha dado que hablar en la última década es la impresión 3D; como por arte de magia, el cabezal del aparato va creando, capa a capa, un objeto de la nada hasta crear una figura tridimensional que puede desde sustituir una manivela hasta usarse como anillo o soporte de pelucas, prácticamente lo que se desee. A finales de la década pasada empezaron a salir a la venta impresoras que prometían que cada uno podría fabricar en su casa el objeto que quisiera, a bajo coste por el tipo de materiales que utilizan (normalmente plásticos) y porque no tiene residuos: se la conoce también como impresión aditiva porque solo utiliza lo necesario para construir el objeto, no sobra nada ni se malgasta nada.
Algunos de sus partidarios más acérrimos la denominan «la tercera revolución industrial» y consideran que llegará a cambiar nuestras vidas. Es probable que sea así, aunque para el grueso de la población parece que no sucederá en un futuro cercano, porque sigue siendo una tecnología algo complicada para utilizarla cada día en casa.
Según Jesús Caro, uno de los fundadores del portal especializado Imprimalia, todavía queda tiempo para que veamos impresoras 3D de forma habitual en los hogares y actualmente es una curiosidad: «no es como meter un folio y darle al botón para que salga la copia».
El mantenimiento tampoco es el equivalente al de una impresora doméstica: «No tiene sentido gastarte 6.000 euros en una impresora profesional para terminar haciendo la cabeza del yeti y poco más. Se puede construir cualquier cosa, sí, pero hay que invertir tiempo y dinero», dice Caro, aunque al preguntarle por el coste aproximado de hacerse con un equipo y empezar a utilizarlo en casa apunta que con entre 200 y 600€ se puede tener un equipo de iniciación «al que tampoco se le vayan a pedir demasiadas prestaciones».
Xabier Cearsolo, jefe de fabricación aditiva de IMH, explica que poco a poco este mantenimiento es cada vez más sencillo: «Las piezas de recambio se están estandarizando y la compatibilidad entre fabricantes es cada vez mayor, lo que reduce mucho los precios. Como con cualquier máquina es imprescindible que esté bien calibrada, lubricada y limpia. Por el resto, los consumibles más comunes son las boquillas y el material, que se debe mantener en condiciones de baja humedad».
Existen tres métodos principales de crear objetos por fabricación aditiva. La primera es la tecnología Fused Deposition Modeling (FDM), que consiste en tomar filamentos de un material y depositarlos sobre una bandeja capa a capa a través de un extrusor. Estos filamentos pueden ser de materiales termoplásticos pero también de nylon, ABS (el plástico que se usa en las piezas Lego) o de origen natural, a base de almidón de maíz, pero también los hay de metal, con aditivos de madera o goma... Es la tecnología más común fuera de las aplicaciones industriales.
El segundo método es Polyjet, la inyección de polímeros que solidifican al contacto con la luz ultravioleta. Las cabezas de impresión proyectan microgotas en sucesivas capas de un grosor de entre 16 y 28 micras y una luz ultravioleta acoplada a la impresora las solidifica. Suele utilizarse para fabricar prototipos.
La tercera tecnología es la Power Bed Fusion (PBF) o fusión de lecho de polvo, que consiste en depositar capas de material en polvo y fundirlas con una fuente de energía (láser o la más potente haz de electrones). Además de servir con materiales plásticos puede utilizar aleaciones metálicas de titanio o de níquel, por lo que es la más usada en distintas industrias, incluida la aerospacial, así como para medicina con instrumental quirúrgico o implantes personalizados.
A estas formas de impresión en breve puede unirse otra, la litografía axial computerizada (CAL), que se está desarrollando aún y que no consiste en imprimir una microcapa sobre otra sino que se fabrica toda la pieza a la vez. Según un estudio publicado a finales de enero en la revista científica Science, se trata de ir girando un contenedor con material sensible a la luz, sobre el que se proyecta un patrón de luz del objeto que se quiera crear con una precisión de 0,3 mm. El material que utilizaría esta técnica es polímeros de acrilato e hidrogel de metacrilato de gelatina, que se solidifica al recibir una cantidad de luz determinada. Con esta técnica se podrían construir estructuras 3D alrededor de una pieza ya existente, algo imposible hoy día.
En la impresora 3D se encuentra el soporte; el material que ejerce de 'tinta'; el cabezal que calienta dicho material para que funda y el extrusor, que va incorporando nuevas capas al material sobre una plataforma demoninada 'cama'. La mayoría de ellos necesita atenciones específicas de mantenimiento como asegurarse de que el extrusor está limpio y que la cama está a la distancia adecuada.
Además, es necesario tener un modelo realizado con un software de edición 3D del objeto que se desea imprimir, lo que requiere de una capacitación técnica, aunque también se puede descargar uno ya diseñado (en webs como Thingiverse hay numerosos modelos).
Entre las ventajas que ofrece este tipo de impresión están el tiempo, ya que, aunque el coste de diseñar la pieza es alto, se realiza en menos tiempo que la fabricación 'tradicional' y, además, solo se paga el material utilizado. Al poder fabricar formas geométricas más complejas, por ejemplo en forma de celdillas, la pieza final es más ligera que si fuera maciza y, en el caso de los automóviles, ese diseño potencia su capacidad de absorción de impactos. Por eso la industria fue durante décadas el terreno donde fue creciendo y mejorando la impresión 3D.
La historia de esta tecnología empezó poco después de las impresoras de inyección de tinta, cuando en 1984 Charles Hull (cofundador de 3DSystems) desarrolló la estereolitografía. Sustituyó la inyección de plástico por la impresión a partir de datos digitales para fabricar prototipos de forma rápida y económica.
Nueve meses desde que di la primera prótesis.
— 🕸️GuilleMartínez #Ayudame3D (@willperman) 24 de abril de 2018
Nueve meses sin saber si le estaría sirviendo.
Hoy, recibo este vídeo.
Por estas cosas sigo a tope con https://t.co/6HJT9oGE0e 💪💜
Pls, compartid para poder continuar con el proyecto, https://t.co/6HJT9oGE0e pic.twitter.com/LPcgjv0UTo
En la primera década del siglo caducaron las distintas patentes de los métodos de impresión en 3D (que poseían grandes empresas como 3DSystems o Stratasys) «y se produjo el despegue de la tecnología porque ha bajado mucho el precio [...] Antes estaba solo al alcance de las empresas dedicadas a hacer prototipos. Profesionales como los arquitectos pueden hacer en sus casas lo que antes se hacía en las empresas», dice Caro.
También cobra fuerza la comunidad 'maker', que potencia la creación o mejora de máquinas a cargo de los usuarios, de forma que no dependan de los fabricantes. Cearsolo explica que buena parte de quienes tienen una impresora 3D en su casa, de momento, son estudiantes jóvenes que estudian una ingeniería. «El uso que estos usuarios da a la impresión 3D es el de fabricar prototipos, piezas de recambio y piezas personalizadas (como partes de drones, juguetes o figuras), incluso piezas con las que mejorar sus propias impresoras 3D2, sostiene Cearsolo.
La creciente popularización de la impresión aditiva ha favorecido el nacimiento de organizaciones cooperativas como e-Nabling, que propone a quienes tengan conocimientos de diseño 3D que diseñen e impriman una prótesis de mano para quienes no pueden permitírsela. La red cuenta con voluntarios en todo el mundo. Más pequeña pero también con el objetivo de crear prótesis para amputados ha nacido la ONG Ayúdame3D, creada por el español Guillermo Martínez, que ha empezado también a fabricar cajas con símbolos de superhéroes para cubrir las bolsas de quimioterapia de los niños en tratamiento siguiendo una idea que surgió en Brasil hace cinco años.
La impresión 3D sigue utilizándose en campos donde ha tenido presencia hace décadas como la automoción, pero cada vez llega más lejos, incluso hasta la Estación Espacial Internacional, donde hay una impresora para poder crear repuestos de piezas y que, además, es capaz de reciclar piezas de plástico para imprimirlas. La idea cobra toda la lógica si se piensa en lo difícil y costoso que es hacer llegar con rapidez al espacio el recambio de una pieza que se ha roto.
En medicina se está generalizando la impresión aditiva en «prótesis personalizadas, principalmente dentro del sector médico y dental«, produciéndose así una prótesis diseñada específicamente para cada paciente. Para Cearsolo, la tecnología tiene ante sí un interesante panorama: «La impresión 3D puede irrumpir en cualquier sector que hace unos pocos años ni se planteaba: cocina, arquitectura, impresión 3D de células madre... Los Centros Tecnológicos y Universidades estamos trabajando para extender la tecnología a nuevas aplicaciones; poder trabajar con nuevos materiales. Con el tiempo veremos cosas nuevas», indica.
En los hospitales de Bizkaia de Osakidetza se trabaja ya con esta tecnología y, en concreto, el Instituto de Investigación Sanitaria Biocruces del Hospital de Cruces tiene las herramientas para la generación de biomodelos que se utilizan para la preparación de intervenciones con réplicas exactas de lo que van a encontrar los cirujanos al operar, explicar a los pacientes qué les sucede y la docencia a nuevos profesionales sanitarios.
En el terreno de la construcción también se imprime más en 3D. Emplea una mezcla de cemento y residuos industriales (como el vidrio) en impresoras gigantes, con las que construir una casa completa en 24 horas. Hay otros usos, no tan gratificantes, como la impresión de armas que disparan balas reales o juguetes sexuales, cuyo uso se pone en duda porque no están homologados ni se garantiza su seguridad.
Una de las aplicaciones más llamativas de esta tecnología es la alimentación. En 2012 nació la empresa catalana Natural Machines, creadora de la impresora 'Foodini': el usuario elige la receta, pone los alimentos en cada una de las capsulas de acero inoxidable que hay en la máquina y la imprime. No hace falta que tengan textura de puré, pudiendo ser cuscús, hamburguesas, arándanos... Eso sí, es un electrodoméstico bastante caro (unos 3.600€).
Aunque esta 'técnica culinaria' no está presente en las cocinas domésticas ni en los restaurantes (con excepciones como el holandés Smink, en Wolvega), sí se está abriendo camino en instituciones como el Basque Culinary Center, donde han llevado a cabo diversas actividades que incluyen la impresión 3D de comida. Hace dos años la empresa byflow lanzó su impresora 'Focus' y desde entonces la utiliza para la iniciativa Food Ink, que organiza eventos culinarios por todo el mundo en los que desde las sillas hasta la comida están impresos en 3D. Por su parte, la empresa británica Dovetailed ha creado -en colaboración con Microsoft- una impresora 3D para frutas que combina zumo con alginato de sodio en polvo para crear pequeñas burbujas comestibles; y la empresa 3D Systems y la chocolatera Hershey han fabricado 'Cocojet', que utiliza el chocolate como material de impresión. Incluso conocidas empresas como Nestlé o Barilla están investigando la aplicación de esta tecnología en sus productos.
Por mucho que llame la atención lo que ya se ha visto, esta aplicación de la tecnología no ha hecho más que comenzar. Algunas de las impresoras de comida ya trabajan con moléculas de carne y la industria pesquera ha empezado a imprimir varitas con mince (proteínas marinas obtenidas de especies que no se suelen comercializar). Una de sus principales aplicaciones es conseguir presentaciones agradables a la vista y al paladar para la gente que tiene problemas para masticar o tragar y ahora debe comer a base de purés. Hace unos meses el departamento de Biosistemas de la Universidad de Lovaina (Bélgica) logró imprimir ositos de goma compuestos de lechuga usando como 'tinta' pectina y células vivas aisladas. Es la primera vez que se consiguen imprimir células vivas de vegetales. Nadie ha podido decir si están ricos o no porque aún no está autorizado su consumo humano.
La moda es otro sector que está despertando a la impresión 3D gracias a los filamentos flexibles como FilaFlex -creado por la empresa alicantina Recreus-, que es un material suave y con gran elasticidad fabricado con elastómero termoplástico. Una de las firmas que lo utilizan es Zer, creada por Anne Castro y Nuria Costa, que consiguieron el premio Samsung EGO Innovation Project el año pasado con la colección CONECT3D, de ropa impresa. El material del que están hechas se puede fundir y reutilizar, lo que reduce los residuos producidos. FilaFlex también lo utiliza la marca Chuic para sus pendientes, algunos de los cuales ha utilizado en ocasiones la presentadora de televisión Cristina Pedroche.
Hay otro terreno en el que puede hacer mucho bien la impresión 3D: la creación de empleo. Para manejar una impresora industrial 3D se necesitan, aparte de tener conocimientos del software que genera la trayectoria de la boquilla que aporta el material; de las propiedades de los plásticos más usados; de mantenimiento; conocer a fondo las propiedades mecánicas de los materiales y manejar programas de diseño de nivel superior. Los expertos consultados coinciden en que en breve harán falta técnicos en impresión 3D, sobre todo para educación, actividades industriales y medicina.
Publicidad
Publicidad
Te puede interesar
El origen de la expresión 'joder la marrana' y su conexión con el vino
El Norte de Castilla
Publicidad
Publicidad
Noticias recomendadas
Esta funcionalidad es exclusiva para suscriptores.
Reporta un error en esta noticia
Comentar es una ventaja exclusiva para suscriptores
¿Ya eres suscriptor?
Inicia sesiónNecesitas ser suscriptor para poder votar.