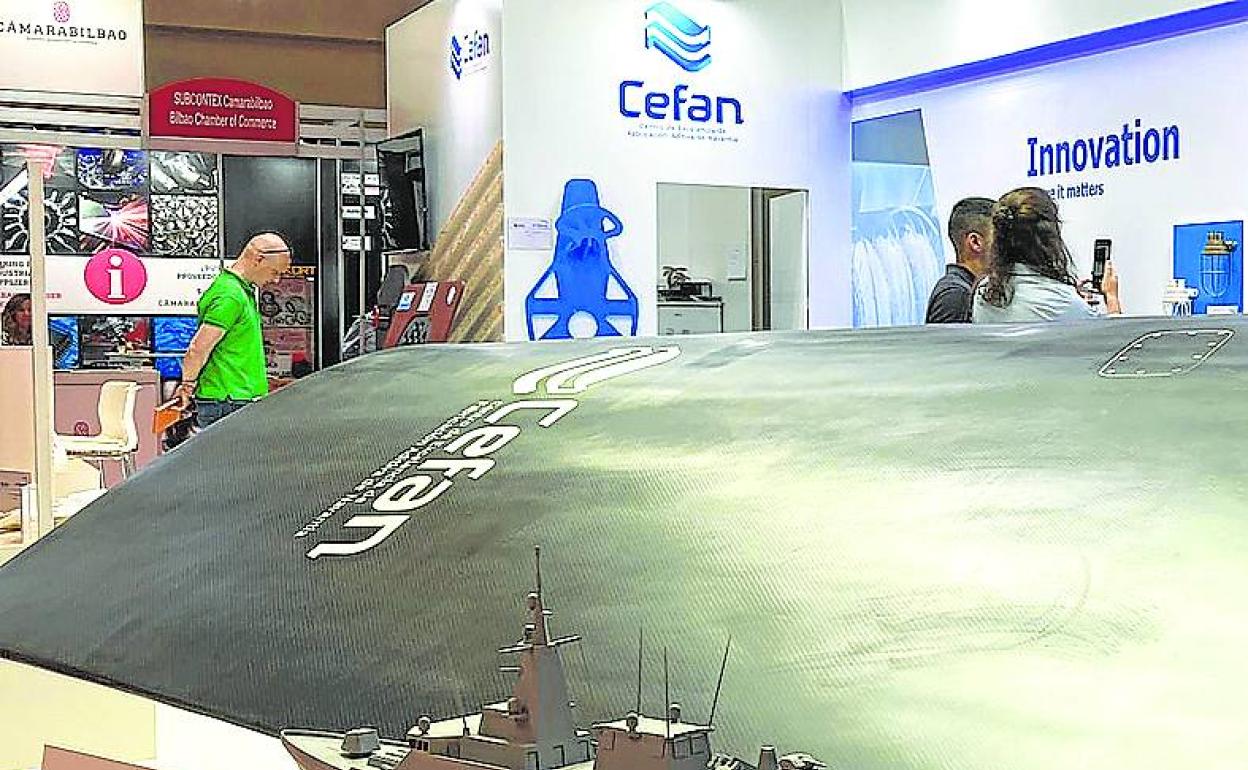
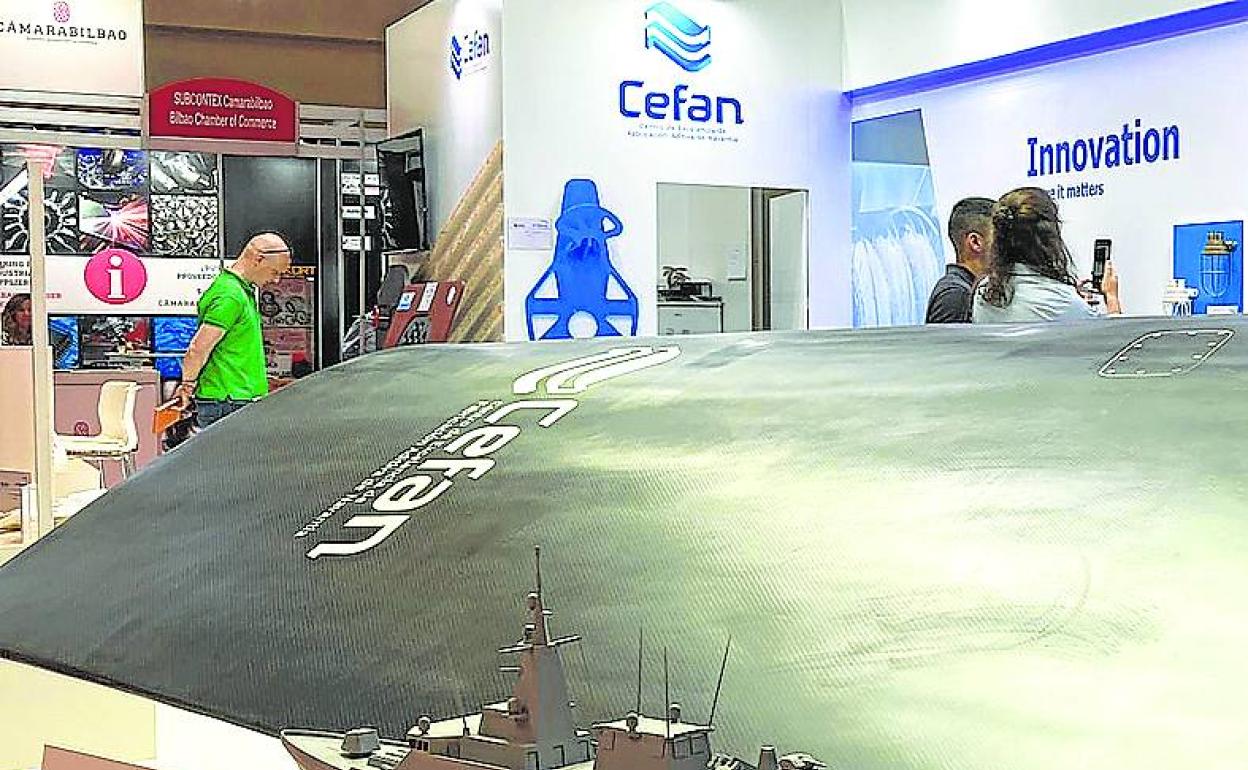
Secciones
Servicios
Destacamos
Edición
sergio llamas
Viernes, 17 de junio 2022, 02:37
La fabricación aditiva todavía representa porcentajes muy escasos en el global de la industria, pero los avances de los últimos años han conseguido dar el salto desde la elaboración de prototipos y tiradas simbólicas, a piezas finales que soportan los requisitos de desgaste, temperatura o ... estrés que requieren sectores tan exigentes como el de la automoción, la aeronáutica o la industria naval.
Así se evidencia esta semana en la Bienal, que suma un centenar de firmas expositoras de 15 países en ADDIT3D, su feria internacional de construcción por impresión 3D. Allí la empresa pública Navantia, que fabrica buques militares y civiles de alta tecnología, expone un timón de corbeta de tres toneladas y media, con un núcleo de acero y una capa exterior de fibra de vidrio. Todo lo demás está fabricado a base de 17 piezas de polímeros de 130 kilogramos, realizadas por fabricación aditiva. «Permite reducir el tiempo de elaboración de un año a tres meses, aumenta las posibilidades de realizar mejoras geométricas y reduce los costes en un 30%», detalló, entre otras ventajas, su representante Fran Abad. El objetivo de la firma ahora es ser tractora en la implementación de esta tecnología en las empresas del sector.
Las mejoras en la fabricación aditiva han sido constantes. En HP destacaron que el sistema resulta más rentable que la inyección en molde para piezas pequeñas, en lotes inferiores a las 150.000 unidades. «Las mejoras de estos años han ido en dos direcciones: hacer que los costes tengan sentido y conseguir que sean piezas completamente funcionales», resumió uno de sus 'business developer', Jacobo Sáenz.
A ello se suma la liberación de patentes que ha extendido la fabricación aditiva metálica, a través de un cordón de soldadura continuo mediante láser que permite generar tochos de metal con cualquier forma interna, incluyendo complicados circuitos de circulación de fluidos. «Hay unidades que se pueden instalar desde los 130.000 euros, y que permiten crear piezas imposibles de otra manera», defendió José María Ferrándiz, de Samylabs.
Todavía falta dar un gran salto: que las industrias apuesten masivamente por este método. «Por el momento los principales clientes de estos equipos son centros tecnológicos y universidades», advirtió Nelson Umbina en el puesto de Sicnova, donde integran estos sistemas en brazos robóticos y en equipos CNC, para conseguir piezas más complejas y soluciones híbridas que combinan el 3D y los mecanizados.
El tamaño de las piezas también está dejando de ser un problema. «En mayo se lanzó Massivit 10000, que permite crear piezas de hasta 1,80 de altura», explicó, por su parte, el comercial de Windforce, Pedro Prieto.
La Bienal también entregó ayer sus premios a la innovación y fabricación digital avanzada, que distinguieron entre otros el timón desarrollado por Navantia con tecnología 3D. El centro de mecanizados AETOS de Zayer, la barra de mandrinar intercambiable de Nicolás Correa, y el amortiguador activo de Soraluce fueron otros diseños premiados.
¿Ya eres suscriptor/a? Inicia sesión
Publicidad
Publicidad
Te puede interesar
Fallece un hombre tras caer al río con su tractor en un pueblo de Segovia
El Norte de Castilla
Publicidad
Publicidad
Esta funcionalidad es exclusiva para suscriptores.
Reporta un error en esta noticia
Comentar es una ventaja exclusiva para suscriptores
¿Ya eres suscriptor?
Inicia sesiónNecesitas ser suscriptor para poder votar.